Get consistent results with professional plastic extrusion techniques
Get consistent results with professional plastic extrusion techniques
Blog Article
A Comprehensive Guide to the Process and Advantages of Plastic Extrusion
In the huge realm of production, plastic extrusion becomes a crucial and highly reliable process. Altering raw plastic into continual accounts, it accommodates a plethora of industries with its impressive flexibility. This guide intends to elucidate the intricate steps associated with this method, the sorts of plastic proper for extrusion, and the game-changing advantages it brings to the industry. The taking place conversation guarantees to unravel the real-world effects of this transformative process.
Recognizing the Essentials of Plastic Extrusion
While it might appear facility at first look, the procedure of plastic extrusion is basically simple - plastic extrusion. It is a high-volume manufacturing strategy in which raw plastic is thawed and formed into a continual profile. The process starts with the feeding of plastic product, in the type of granules, powders, or pellets, right into a heated barrel. The plastic is then melted utilizing a combination of warm and shear, used by a turning screw. When the molten plastic gets to completion of the barrel, it is compelled with a little opening referred to as a die, forming it right into a desired form. The shaped plastic is after that cooled down, solidified, and cut right into wanted lengths, completing the process.
The Technical Refine of Plastic Extrusion Explained
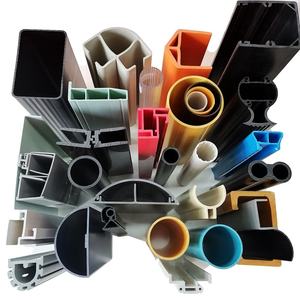
Types of Plastic Suitable for Extrusion
The option of the appropriate kind of plastic is a vital element of the extrusion procedure. Various plastics provide unique properties, making them a lot more suited to certain applications. Recognizing these plastic kinds can substantially improve the extrusion procedure.
Comparing Plastic Extrusion to Other Plastic Forming Methods
Recognizing the sorts of plastic ideal for extrusion leads the way for a more comprehensive conversation on how plastic extrusion stacks up versus other plastic developing methods. These include injection molding, strike molding, and thermoforming. Each technique has its special usages and benefits. Shot molding, as an example, is superb for developing detailed parts, while impact molding is excellent for hollow items like bottles. Thermoforming excels at forming shallow or large components. Plastic extrusion is unmatched when it comes to developing continual accounts, such as seals, gaskets, and pipes. It also permits for a consistent cross-section along the size of the item. Hence, the imp source choice of approach largely relies on the end-product requirements and requirements.
Secret Advantages of Plastic Extrusion in Manufacturing
In the world of manufacturing, plastic extrusion offers numerous significant advantages. One noteworthy advantage is the cost-effectiveness of the procedure, that makes it a financially appealing production technique. Additionally, this strategy provides premium product versatility and boosted manufacturing speed, thus enhancing overall production performance.
Affordable Manufacturing Approach
Plastic extrusion leaps to the forefront as a cost-efficient production technique in manufacturing. In addition, plastic extrusion calls for less power than traditional production methods, adding to lower functional expenses. Generally, the economic advantages make plastic extrusion an extremely appealing choice in the manufacturing sector.

Superior Product Adaptability
Beyond the cost-effectiveness of plastic extrusion, another substantial benefit in producing lies in its superior item versatility. This makes plastic extrusion an excellent remedy for industries that require tailored plastic components, such as automobile, construction, and packaging. In significance, plastic extrusion's item flexibility fosters development while boosting functional efficiency.
Enhanced Manufacturing Speed
A substantial advantage of plastic extrusion depends on its boosted manufacturing speed. This production process enables high-volume production in a reasonably brief time period. It can generating long, continual plastic profiles, which significantly reduces the production time. This high-speed manufacturing is particularly beneficial in markets where huge amounts Source of plastic components are required within limited due dates. Couple of various other manufacturing procedures can match the rate of plastic extrusion. Furthermore, the ability to maintain regular high-speed manufacturing without compromising item high quality establishes plastic extrusion apart from various other techniques. The improved manufacturing speed, consequently, not just allows makers to satisfy high-demand orders but additionally adds to raised efficiency and cost-effectiveness. This advantageous feature of plastic extrusion has made it a preferred choice in countless industries.
Real-world Applications and Impacts of Plastic Extrusion
In the world of manufacturing, the method of plastic extrusion holds profound relevance. This procedure is commonly made use of in the production of a selection of items, such as plastic tubing, window frames, and climate removing. As a result, it greatly influences sectors like construction, product packaging, and automobile markets. Moreover, its influence encompasses daily items, from plastic bags to tooth brushes and disposable flatware. The economic advantage of plastic extrusion, largely its cost-effective and high-volume result, has actually reinvented production. The ecological influence of plastic waste stays an issue. Consequently, the industry is persistently pursuing advancements in biodegradable and recyclable materials, showing a future where the benefits of plastic extrusion can be preserved without jeopardizing environmental sustainability.
Verdict
To conclude, plastic extrusion is a highly reliable and efficient technique of transforming basic materials right into diverse products. It provides many benefits over other plastic forming methods, including read more cost-effectiveness, high result, very little waste, and layout adaptability. Its impact is greatly really felt in various markets such as building and construction, automobile, and customer products, making it a critical procedure in today's production landscape.
Diving much deeper right into the technological process of plastic extrusion, it starts with the choice of the appropriate plastic product. As soon as cooled down, the plastic is cut right into the required lengths or wound onto reels if the item is a plastic film or sheet - plastic extrusion. Contrasting Plastic Extrusion to Other Plastic Forming Techniques
Comprehending the types of plastic ideal for extrusion leads the way for a more comprehensive conversation on just how plastic extrusion stacks up against various other plastic forming approaches. Couple of other manufacturing processes can match the speed of plastic extrusion.
Report this page